Become an Expert in Work Order, Job Orders, or Shop Orders within Manufacturing Software
Learn:
Overview or Shop Floor or Work Orders
Definition and Details of Work Order or Shop Floor Order
Benefits of Using Work Orders
Key Features of SimpleManufacturing™ Work Order Management Module
Material-Related Features of SimpleManufacturing™ Work Orders
Process-Related Features of SimpleManufacturing™ Work Orders
Accounting-Related Features of SimpleManufacturing™ Work Orders
Continue Reading More…..
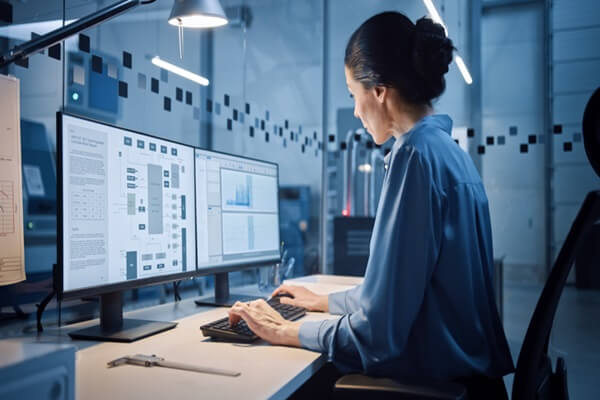
Work Order Overview
Work order, job order, work request, service request, or shop order has numerous meanings and applications. The general definition of a Work Order is found here. For ERP Software, this is best defined as an order to the shop to perform an activity. For example, manufacturing a product, item, or assembly is the most common. Reworking, upgrading, or revising a product, item, or assembly is another common use of work orders.
The activity that begins a task is initiating a shop order. Additionally, the shop order identifies the work to be done by providing all the information necessary to complete the task. Furthermore, collecting data along the process captures the history of the work performed.
What Information does a Job Order Contain?
A Job Order identifies the task to be performed for ERP Software, is typically the Part to be assembled, reworked, serviced, or upgraded, the Quantity needed, and Due Date.
Additionally, identifying the material required is simple as it is the centralized source of material requirements. It includes the quantities in which the materials are needed, descriptions, costs, and the just-in-time (JIT) material need date.
Furthermore, each job order contains process-flow instructions, a Router, a Traveler, or Job Card. These instructions provide step-by-step instructions and include identification of work centers and equipment requirements.
What are the Benefits of Using Shop Orders?
Identifying and Resolving Shortages
Running the material requirements planning function identifies expected shortages since each shop order has a material requirement, process flow, and due date element. Addressing the expected shortages resolves issues before they occur – fail to plan, plan to fail.
Improving Shop-Floor Efficiency
Fulfilling shop orders is simple at every phase of its lifecycle, including releasing, picking material, recording quantity, filling shortages, recording labor entries, and completing receipts.
Streamline ERP Production and Materials
A single-click function explodes Multi-Level BOMs into the required parent and child shop order to see the assemblies and individual material and labor requirements.
Real-Time Visibility
A single dashboard interface for shop orders provides efficient access to shop order information, real-time progress reports, material shortages, and other related data. Real-time tracking identifies shop orders falling behind schedule. Addressing shop orders falling behind schedule promptly improves production times.
Repeatability
Copying shop orders ensures the repeatability of an assembly, finished good product, or service’s assembly, construction, production, or repair. The exact result is facilitated using the same material, instructions, process flow, and equipment. In addition, consistently providing clients with the same products fosters their confidence.
Integration with Financials
Behind-the-scenes accounting transactions related to shop order management provide real-time financials such as Accrued and Current Account Payables for materials on order and received in support of shop order efforts. Furthermore, balance sheets provide current raw material, work-in-process (WIP), and finished goods dollars. Additionally, recording of labor times of shop orders provides real-time financials for Accrued Salaries and is included within work-in-process (WIP) and costing.
Key Features of SimpleManufacturing™ Work Order Management?
Consolidated Visibility and View
Manage all regular repair, rework, and stock job orders in a single dashboard.
Subcontracting Work Order Classification
Classifying Work Orders between Turnkey and Consignment clarifies subcontractors’ material responsibilities. Requiring the contract manufacturer to procure all materials and services to complete the Customers’ order is considered a Turnkey Shop order. Customers providing the material to complete an order are considered a Consignment Shop Order.
Automation
Effortlessly create Shop Orders from Sales Orders, Material Requirements Planning Output, Quality Repairs, and Kanban / Minimum Inventory Levels.
Depending on the business type, processes, or strategies, Shop Orders can be linked to a specific line item within a Customer’s Order. This might be referred to as the “Job Shop” approach. For example, higher volume, mixture, or complexities of products manufactured might utilize the Material Requirements Planning process to create Work Orders. In addition, manufacturing defects or inspection failures might warrant the creation of rework work orders. Lastly, Kanban or other approaches to inventory management might warrant work order creation to replenish low inventory levels.
Quality and Compliance Requirements
The specific QA or Industry Standard requirement passed on by the Customer can be identified on each work order. Additionally, serialization requirements can be included within each work order. The serialization can be based on customers and those generated by manufacturers to identify products or assemblies manufactured uniquely. Lastly, work orders can identify packaging, preservation, and labeling requirements. Convenient when these requirements are identified within Customer Orders.
Flexibility
The partial completion of Shop Orders within any step of the process flow can compensate for the demands of customers, revenue goals, and product releases. In addition, this flexibility helps businesses, subcontractors, and manufacturers minimize the impact of change.
Key Material-Related Features of SimpleManufacturing™ Work Order Management?
Kitting / Pulling Inventory
Many options exist depending on the business type and processes when kitting or pulling material required. For example, the material can be pulled before release to the shop floor or at specific work centers along the process flow, typical of the as-needed or JIT approach. Additionally, an Auto-Kit feature is available to transact material into WIP without the need for any verification of inventory.
Kitting and Pulling of inventory use the FIFO (First-In, First-Out) method to identify the order in which the material should be consumed. Still, it is also flexible enough to allow deviations from this method. This method captures the actual costs of material for each job order.
Various Identification methods of Material are available such as:
Internal Part Number,
Customer Part Number,
Component Manufacturer and Part Number
Component Supplier / Vendor and Part Number
Material Requirements Source: Bill of Material
The shop order material requirements are created directly from the Bill of Material. In addition, any alternates and substitutes included within the Bill of Material are identified for convenience. Deviations from the material requirements used can be added to the shop order. When used and appropriate, this flexibility minimizes the impact of completing the work order on time while capturing all material consumption within a specific shop order.
Material Transaction Logs
Quickly identify the material consumed within each work order, the manufacturer or vendor name, and part numbers and quantities. For traceability purposes, this information also contains the material purchase order, purchase order line, receipt dates, date codes, lot codes, and any other characteristics added at the time of material receipt.
Excess Material Separated from Required Material
Easily track and manage kitted or pulled material exceeding the required amount. Kitting excess material is a practice that some businesses follow to ensure that enough replacement material is immediately available for issues during setup or other processes that may require extra material than initially planned. Embracing such practice requires unused excess material to be returned to inventory after completing the work order. A simple audit of the unused material and a click of a button within SimpleManufacturing™
are all required to return the unused product to inventory.
Key Process-Related Features of SimpleManufacturing™ Work Order Management?
Router / Traveler / Process Flow Source: Bill of Material Information
The work order router, traveler, and process flow are created directly from the Bill of Material definition at work order creation. This router defines process flow, instructions, tools, fixtures, and quality inspections. Each routing step can Link 1st piece inspections, First-Article Inspections, and other in-process quality inspection requirements. Any changes to the router can be made during the initial processing of the work order. Upon completion of the work order, changes can be incorporated into the original Bill of Material so that all subsequent work orders follow the as-built process.
Labor Transactions
Recording labor times at each process step is simple for operators.
Completion Transactions
Recording the completion and quantities of each router step is another simple process for operators.
Real-Time Visibility
Viewing of shop-floor status is only a Single-Click away. In addition, the real-time status of the work orders released, in-process, and currently located based on the planned process flow helps maintain the schedule.
Key Financial-Related Features of SimpleManufacturing™ Work Order Management?
Automated Accounting Transactions
All accounting transactions are carried out behind the scenes. For example, all Material transactions move dollar amounts between Current Asset accounts, such as raw materials, work-in-process (WIP) and finished goods. Likewise, all Labor transactions added based on the Operator recording of the labor portion of Work Orders move dollars between Current Assets (WIP) and current liabilities such as accrued salaries.
Automated Costing Transactions
Completion of each unit within a work order is based on per unit material and labor WIP costs.
Choosing SimpleManufacturing™ as your next Shop Floor Management Solution
The SimpleManufacturing™ Work Order Management Module is an efficient and powerful approach to managing Work Orders. Viewing work order status from start to finish and providing real-time progress at any time removes the uncertainty of Work Order status. In addition, providing an accurate inventory account eliminates the uncertainty of material demands. Furthermore, recording labor times at each process step completes the data requirements for to cost of each unit.
In summary, its automation processes help facilitate that the correct work orders are created for the right quantities and in a just-in-time manner. Recording the material and labor of each work order produces an accurate calculation of the Cost of Goods Sold (COGS). Simplify manufacturing by using SimpleManufacturing™.