Work Order Management
Transform Chaos into Order: Master Work Order Management in Manufacturing.It’s all about planning, executing, and monitoring the production process to ensure efficiency, accountability, and cost control
Work Order Management is vital in manufacturing for several reasons:
Efficiency Boost:
It streamlines operations by tracking and scheduling tasks, reducing downtime and improving productivity.
Optimal Resource Use:
It ensures that materials, equipment, and personnel are used effectively, preventing waste and delays.
Cost Control:
By monitoring progress and resource consumption, manufacturers can avoid cost overruns and keep budgets in check.
Quality Assurance:
Detailed tracking helps maintain high-quality standards throughout the production process.
Compliance:
Accurate records are essential for meeting industry regulations and standards.
Customer Satisfaction:
Timely and efficient work order management leads to on-time delivery, boosting customer trust and satisfaction.
A robust Work Order Management system keeps the manufacturing process smooth and efficient, ensuring that all aspects of production are well-coordinated and under control
Work orders in manufacturing are like detailed blueprints for getting things done on the production floor. They serve as instructions that outline specific tasks to be completed, materials required, and the timeline for each step. Here are some key components and purposes of work orders:
Details of Tasks:
Work orders specify what needs to be done, who will do it, and how it will be done.
Materials and Resources:
They list the materials, tools, and resources required for the tasks.
Timeline:
Work orders often include start and end dates, helping ensure the work is completed on schedule.
Quality Control:
They may include quality checkpoints to ensure that the product meets the required standards.
Documentation:
Work orders serve as a record for tracking the progress and completion of tasks, which is crucial for audits and continuous improvement.
In essence, work orders are essential for maintaining organization, efficiency, and quality in the manufacturing process.
What is an ERP Software without Work Order Management?
That is why it is included in SimpleManufacturing™!
Our Work Order Management Features
Common Work Order Information
Part Number, Description, Revision Level, Quantity To Produce and Due Date
Material Issue
Record and Track Material Necessary for the Completion or Work Orders. Automatic Transactions Entered Moving Stock to Work-In-Process (WIP) Inventory Location
Shortages / Excess Material
Identify Shortages Of Material Required to Complete Work Orders. Record and Track Excess Material Consumed
Material and Labor Accountability
Record and Track Material and Labor Costs of Each Work Order
Transaction History
View Material and Labor Transaction History
Router / Traveler / Process Flow
Each Work Order Inherits Router from Bill of Materials and Used Throughout the Manufacturing Process
Vendor Part Numbers
Record and View All Vendor Part Numbers and Quantities Consumed By Work Order
Serial Numbers
Manage and Issue Unique Serial Numbers to Work Orders
Actual Costing
Unit Costing Based on Material Actual Costing and Labor Costs. Each Completed Unit has a Unit Cost to Produce
First-In, First-Out (FIFO)
First-In, First-Out Order of Available Stock for Material Issuing
Auto-Kit Options
Automatically Issue Material in Required Quantities for Available Stock using FIFO Method
Emailing Shortages
Single Click Email of All Material Shortages of a Work Order
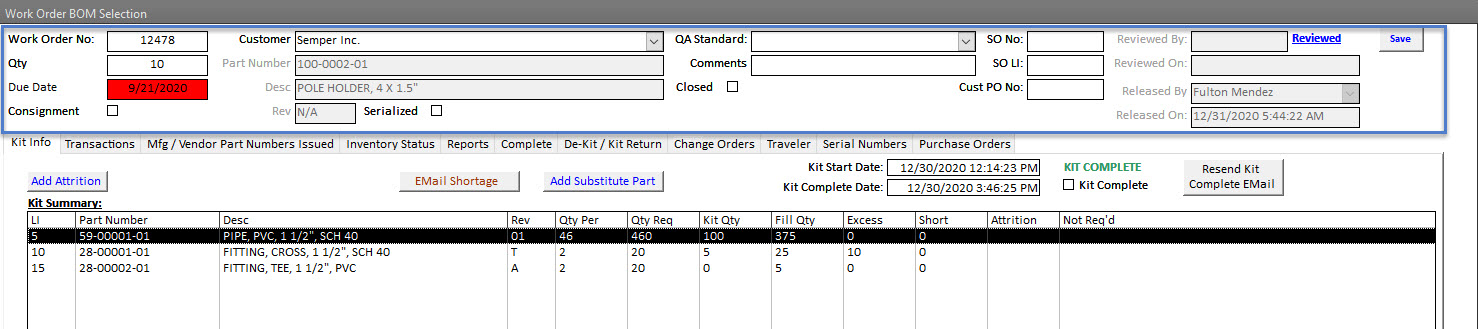
Call Now for a Free DEMO!
858-335-6421