Supplier Management
Supplier or Vendor Management, known as Supply Chain Managment is critical process that involves the selection, evaluation, and management of suppliers to ensure the consistent delivery of high-quality materials and components for production.
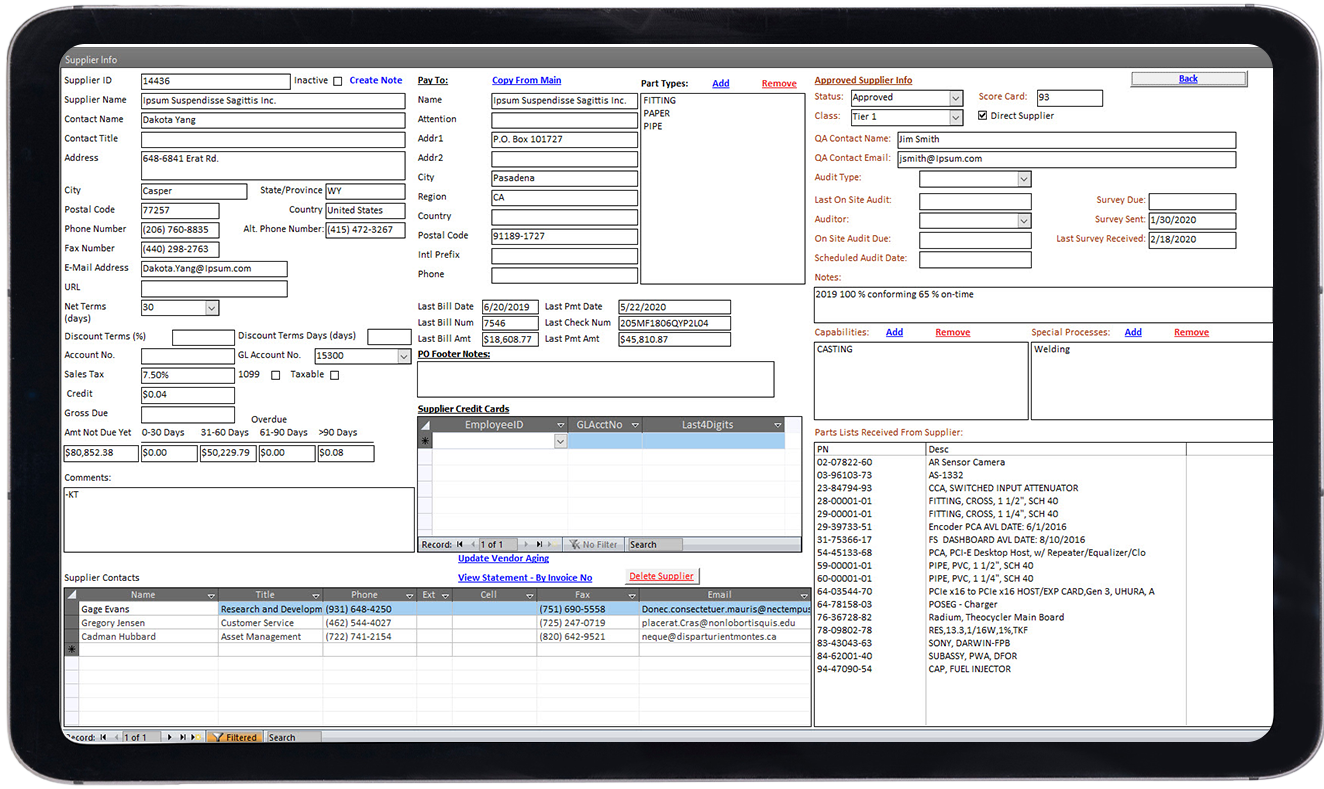
Effective supplier management directly influences the efficiency, cost-effectiveness, and quality of the products being manufactured.
Here are the key elements of supplier management in manufacturing:
Supplier Selection
- Criteria: Selecting the right supplier involves evaluating their capacity, quality standards, pricing, delivery schedules, and reliability.
- Research Analysis: Gathering information about potential suppliers, including their reputation in the market, financial stability, and ability to scale with demand.
Supplier Evaluation
- Performance Metrics: Regularly measuring suppliers based on performance indicators such as quality, on-time delivery, communication, and compliance with contractual terms.
- Audits And Inspections: Conducting regular audits to ensure the supplier adheres to agreed standards and can continue to meet production needs.
Supplier Relationship Management (SRM)
- Collaboration: Building strong, transparent, and mutually beneficial relationships with suppliers to enhance communication and collaboration.
- Long-Term Partnerships: Moving beyond transactional relationships to foster long-term partnerships that can lead to better pricing, reliability, and innovation.
Risk Management
- Risk Assessment: Identifying potential risks in the supply chain, such as delays, financial instability of suppliers, or geopolitical issues affecting supply.
- Contingency Planning: Developing contingency plans to mitigate disruptions, including sourcing alternatives or creating buffer inventories.
Contract Management
- Clear Terms: Defining clear terms of the contract, including delivery schedules, pricing structures, quality standards, and penalties for non-compliance.
- Regular Reviews: Ensuring that contracts are regularly reviewed and updated to reflect changing market conditions or manufacturing needs.
Supplier Development
- Improvement Programs: Working with suppliers to improve their processes and capabilities, ensuring they can consistently meet evolving demands.
- Training And Support: Providing training or resources to suppliers to help them meet quality or regulatory standards.
Performance Feedback And Communication
- Open Communication: Maintaining open lines of communication with suppliers to address issues quickly, resolve conflicts, and share expectations clearly.
- Feedback Loops: Offering feedback on the supplier’s performance to encourage continuous improvement.
Technology Integration
- Supply Chain Management Software: Utilizing technologies like ERP (Enterprise Resource Planning) and SCM (Supply Chain Management) software to streamline supplier communication, order tracking, and inventory management.
- Data Sharing: Sharing relevant data with suppliers to improve forecasting, production planning, and overall supply chain efficiency.
Cost Management
- Negotiation And Cost Control: Negotiating favorable terms while maintaining fair and sustainable pricing for both parties.
- Total Cost of Ownership (TCO): Considering not only the initial cost of goods but also factors like delivery costs, quality, warranty, and after-sales service.
Sustainability And Compliance
- Sustainability Standards: Ensuring suppliers meet sustainability criteria, which can include environmentally friendly production methods, ethical sourcing of materials, or adherence to labor laws.
- Compliance with Regulations: Making sure suppliers adhere to relevant local and international standards and regulations.
By managing suppliers effectively, manufacturers can achieve greater operational efficiency, reduce costs, and ensure the high quality of their final products. Supplier management also plays a key role in ensuring that the supply chain remains resilient and adaptable to changing circumstances.
Simple Manufacturing
Our Supplier / Vendor / Supply Chain Module Features
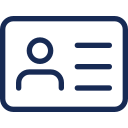
Common Supplier Information
Supplier Name, Address, Phone, Email, Website URL, Classifications – Small Business, Veteran, Women and Minority Owned
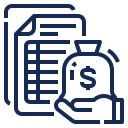
Pay To or Account Payable Information
Mailing Address, Wire Transfer, Electronic Transfer Details
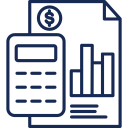
Payment Terms / Accounting Setup
Net Terms, Early Payment Terms, Credit Amount, 1099, Taxable Status, Default Chart Of Account
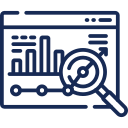
Real-Time Accounting Status
Current AP Status, Last Paid Information
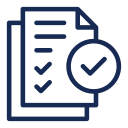
Approved Supplier Details
Approval Status, Audit Type and Schedule, Real-Time Rating / Score Card, Risk Level, Special Processes, Quality Contact Information
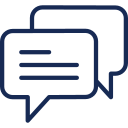
Supplier Contacts
Manage unlimited number of Supplier Contacts and Contact Information

Performance Reporting
Single-Click Features to View and Email On-Time Delivery Summary, Inspection Yields, Score Card and Ratings
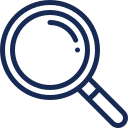
Fast Supplier Searching
Utilize Comprehensive Search options to find suppliers of interest
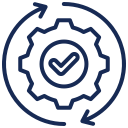
Automation / Reports
Receive AP Aging Reports on a User-Defined Frequency, Purchasing History, Statements