Purchase Order Management
Purchasing management in manufacturing plays a crucial role in ensuring that the necessary raw materials, components, and services are available for production while keeping costs controlled and maintaining product quality.
All activities and processes that enable manufacturers to source materials, manage supplier relationships, and coordinate delivery schedules are all included in our Purchase Order Management module.
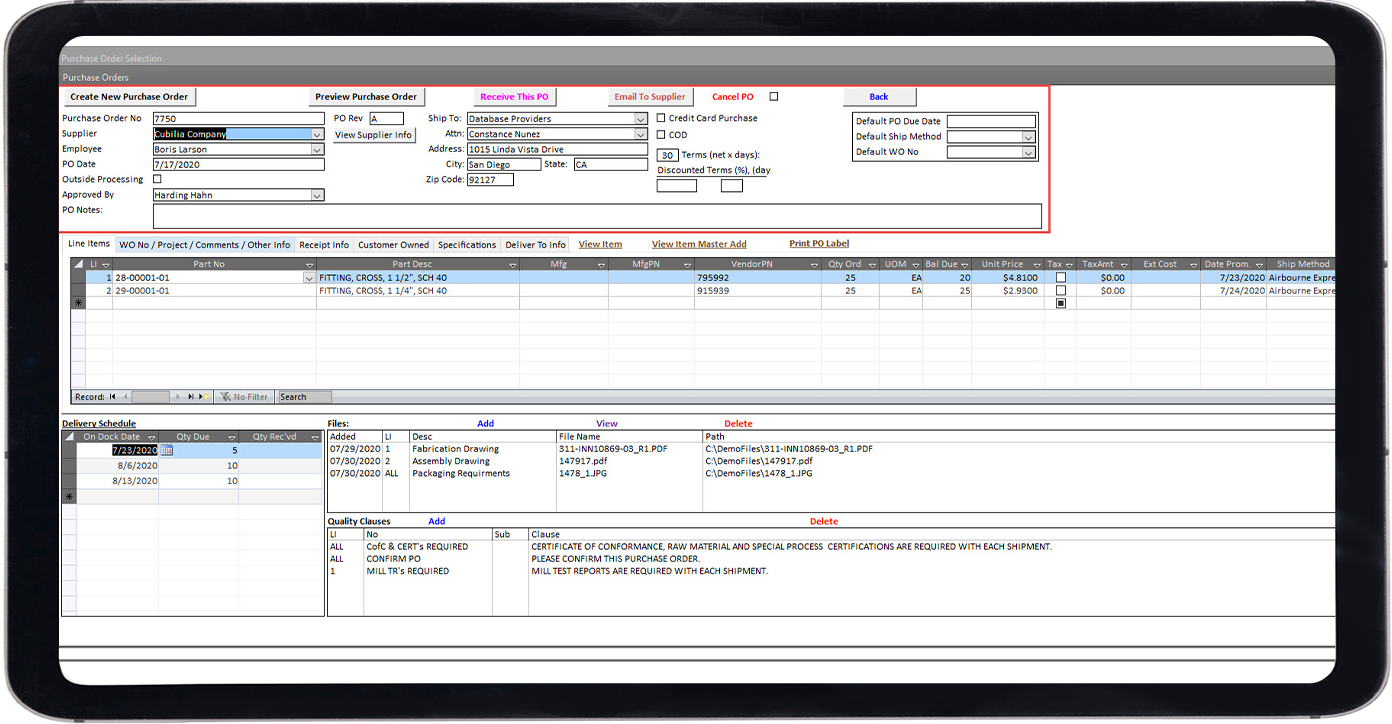
Purchase orders (POs) are vital in manufacturing because they formalize the purchasing process, ensure clarity between buyers and suppliers, and provide several operational and financial benefits.
Here’s why POs are so important in manufacturing:
Clarity and Documentation
Clear Communication:
A PO outlines specific details such as
item descriptions, quantities, prices,
delivery dates, and payment terms.
This clarity helps prevent
misunderstandings between the
manufacturer and the supplier.
Legal Protection:
A PO serves as a legally binding
contract between the two parties. If
there are disputes about the order, the
PO can be used to resolve them,
protecting both the manufacturer and
the supplier.
Inventory Control and Planning
Inventory Management:
Purchase orders allow manufacturers to keep track of materials ordered and when they are expected to arrive. This information helps in managing inventory levels and ensuring that production doesn’t experience delays due to material shortages.
Production Scheduling:
With accurate POs, production planners can schedule tasks and allocate resources more effectively, knowing when materials will arrive.
Cost Control
Budgeting:
Purchase orders help manufacturers track spending against budgeted costs. When prices and quantities are confirmed before an order is placed, it helps in forecasting and managing costs more efficiently.
Price Accuracy:
POs specify agreed-upon prices, reducing the risk of discrepancies in pricing or unexpected cost increases when the invoice arrives.
Accountability and Transparency
POs create a documented trail of all purchasing activities. This helps with audits, compliance checks, and financial reporting, providing transparency throughout the purchasing process.
Internal Control:
By requiring a PO for every purchase, companies can enforce internal controls, ensuring that purchases are approved before being made, which reduces unauthorized spending.
Supplier and Vendor Relationship Management
Consistency:
Using POs ensures consistency in transactions with suppliers. Suppliers also appreciate having a clear document that outlines the exact terms of the order, which can help build stronger, more reliable relationships.
Dispute Resolution:
If any issues arise with deliveries, quality, or quantities, the PO can be referenced to resolve the problem, ensuring that both parties adhere to the agreed terms.
Operational Efficiency
Automated Systems Integration:
Many companies use Enterprise Resource Planning (ERP) systems to automate PO creation, tracking, and approval processes. This integration speeds up the ordering process and reduces human errors in tracking and paperwork.
Order Accuracy:
Since POs include detailed information, there’s less room for mistakes in terms of what’s ordered and delivered. This leads to fewer instances of receiving incorrect materials or quantities.
Legal and Compliance Assurance
Regulatory Compliance:
In certain industries, regulatory compliance is essential, and purchase orders help ensure that all purchases are documented and tracked properly.
Tax and Customs Requirements:
POs can help ensure compliance with tax laws and customs regulations, especially when importing materials from international suppliers.
Payment and Financial Management
Invoice Matching:
When an invoice arrives, it can be matched against the PO to verify that the quantities, prices, and terms are correct. This ensures that only authorized and accurate purchases are paid for, reducing the risk of fraud or errors.
Cash Flow Management:
By knowing the terms of the PO and when payments are due, manufacturers can better plan for cash flow, managing expenses in alignment with production schedules.
Risk Mitigation
Supply Chain Risk Management:
With a purchase order in place, the manufacturer has a formalized agreement on when materials will be delivered. If there’s a delay or issue with the supplier, the PO can help address the situation quickly and mitigate risks to production.
Consistent Terms and Conditions:
The PO ensures that both parties are on the same page regarding payment terms, delivery schedules, and other conditions, helping to prevent surprises later in the process.
Performance Metrics and Supplier Evaluation
Tracking Supplier Performance:
By monitoring the fulfillment of POs, manufacturers can assess supplier reliability. On-time deliveries, order accuracy, and product quality can all be measured against POs to evaluate supplier performance.
Negotiation Leverage:
Historical PO data can be used to negotiate better prices or more favorable terms with suppliers, especially if there’s a long history of successful transactions.
Purchase Order Management is foundational to manufacturing operations as it provides structure, accountability, and control. That is why it is included in SimpleManufacturing™!
Our Purchase Order Management Features
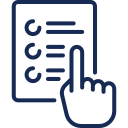
Common Purchase Order Information
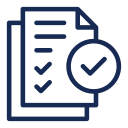
Common Purchase Order Line-Item Information
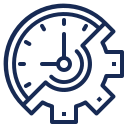
Delivery Schedule
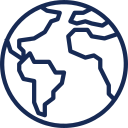
Specification / Standard Requirements
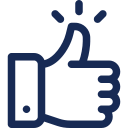
Quality Clauses
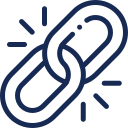
Link Files to Purchase Order
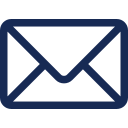
Emailing With Ease
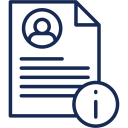
Work Order / Job Number
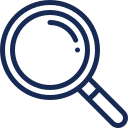