Quality Assurance Management
Efficiently manage NonConformances, Corrective Actions, Employee Training, Document Control, Internal Auditing, Calibration, Risk, and Management ReviewConsolidating these critical quality-related processes into a single module enables real-time status and timely response to undesired situations.
It eases the auditing process and data collection of outside agencies.
The convenience of having this information in a single solution is priceless!
Quality Assurance (QA) in manufacturing is a systematic process designed to ensure that products meet or exceed customer expectations and regulatory requirements. Here are some key aspects of QA in manufacturing:
Key Aspects of Quality Assurance:
Preventive Measures:
QA emphasizes preventing defects rather than just detecting them. This involves designing robust processes, training employees, and maintaining equipment.
Standards and Specifications:
QA ensures that products comply with industry standards, customer specifications, and regulatory requirements. This includes adhering to ISO and AS9100 standards, ASTM, and other relevant guidelines.
Quality Control (QC):
While QA focuses on the overall system, QC is a subset that involves testing and inspecting products to ensure they meet quality criteria. QA oversees and ensures QC processes are effective.
Continuous Improvement:
QA involves continuously analyzing and improving processes to enhance product quality and efficiency. This often includes using methodologies like Six Sigma, Lean Manufacturing, and Total Quality Management (TQM).
Documentation and Record Keeping:
QA processes require meticulous documentation of procedures, inspections, and test results. This documentation is crucial for traceability, compliance, and continuous improvement.
Employee Training and Engagement:
Effective QA programs involve regular training and engagement of employees to foster a culture of quality awareness and responsibility.
Supplier Quality Management:
QA extends to managing the quality of raw materials and components from suppliers. This includes supplier audits, quality agreements, and incoming inspections.
Customer Feedback:
Incorporating customer feedback into QA processes helps identify areas for improvement and ensures that products meet or exceed customer expectations.
In summary, QA in manufacturing is a holistic approach aimed at producing high-quality products, reducing waste, and ensuring customer satisfaction. It’s an ongoing commitment to excellence and continuous improvement
The Convenience and Efficiency of Having Common Quality Assurance Processes in one module is Priceless!
That is why it is included in SimpleManufacturing™!
Our Quality Assurance Management Features

Inspection and NonConforming Material
A Simple, Effective, and Easy process to record and track all inspections and non-conforming material and products

Corrective Action
Record, Manage and Track all corrective actions. 8D and 5 Why Methodology

Training
Record and Track Employee Training, Manage Employee Training Requirements and Entire Organizations Training Program

Control of Documents
Full Cycle, Electronic and Automated Process and Features to Add, Review, Approve, Release and Obsolete Documents

Internal Auditing
Plan Internal Audit Schedule, Execute Audit and Record Results, Track Actions and Follow Up To Closure

Control of Calibrated Devices
Manage All Calibrated Devices, Internal or 3rd Party Calibration Results and Certifications with Automated Alerts

Preventive Maintenance
Manage PM Plan, Records, PM Inventory, Labor, Unplanned Downtime, Repairs With Automated PM Alerts

Contract Review
Electronic Review Process of Customers Orders using a Functional Group Approach
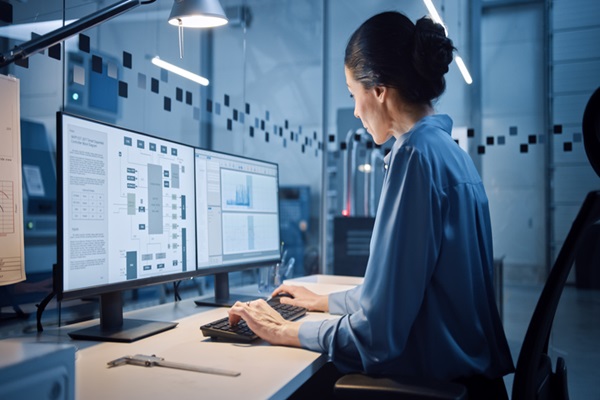
Control Plans
Define Inspection Points, Details, Pass / Fail Criteria Per Operational Step
Call Now for a Free DEMO!
858-335-6421