Item and Part Management
The Item Master, or Part Master is an integral component of ERP systems, providing seamless integration with other modules such as bill of materials, inventory, work orders, routing, invoicing, and data management. This integration fosters synergy between various functions within an organization.
Having accurate, complete, and well-defined Items or Parts have a pivotal role in streamlining operations, optimizing inventory control, and facilitating efficient supply chain management.
Why is an item master important in manufacturing?
An Item Master is essential in the manufacturing sector for a multitude of reasons.
Consistency and accuracy:
First and foremost, it guarantees consistency and accuracy by ensuring that every department has access to the same reliable information about items. This significantly reduces errors and inconsistencies that can disrupt operations.
Inventory management:
Furthermore, it plays a pivotal role in inventory management by effectively tracking inventory levels, preventing stockouts or overstocking, and optimizing inventory turnover for better efficiency.
Cost control:
Cost control is another critical aspect, as it provides comprehensive cost information for each item, which is invaluable for budgeting, financial planning, and maintaining control over expenses.
Procurement and Purchase Orders:
Additionally, an Item Master facilitates supplier management by storing vital supplier information, making it easier to nurture relationships and assess supplier performance. In terms of production planning, it streamlines processes by offering detailed item specifications and availability, allowing for more efficient planning.
Bill of Materials (BOM):
Item Masters are intricately linked to Bill of Materials (BOM) structures, providing the foundational data required to assemble finished products. The BOM specifies the components, quantities, and routing instructions for manufacturing processes, seamlessly integrating with the Item Master’s data.
Regulatory Compliance:
Lastly, it ensures regulatory compliance by confirming that all items meet necessary standards and quality requirements.
Beyond these advantages, a well-maintained Item Master enhances communication across teams, fosters collaboration, and strengthens decision-making processes. By centralizing item data, it empowers manufacturers to swiftly adapt to market changes and respond to customer demands, ultimately driving operational efficiency and boosting profitability.
Features of Our Item / Part Master
Common Fields - Item or Part Number, Revision Level Description, Unit of Measure
Category - Raw Material, Sub-Assembly, Finished Good
Part Type - Make, Buy, Phantom
Classification - Inventory, Expense
Regulatory Identification - FAA, FCC, CS, UL
Cost Control - Standard Cost
Shelf Life Identification - Expiration Period
Approved Vendor List - Vendor Part Numbers
Specialty Attributes - Material, Size, Value, Tolerance, ROHS
Default Inventory Accounts - Raw Material, Finished Goods, WIP
Default Income Accounts - Revenue, COGS
Default Expense Accounts
Link Websites, Datasheets, Files to Item
View Inventory Levels, Purchase Order History, Lead Times
Automated Tracking of Changes Made to Order - Who, What, When
Comprehensive Searching Capabilities for Quick Access
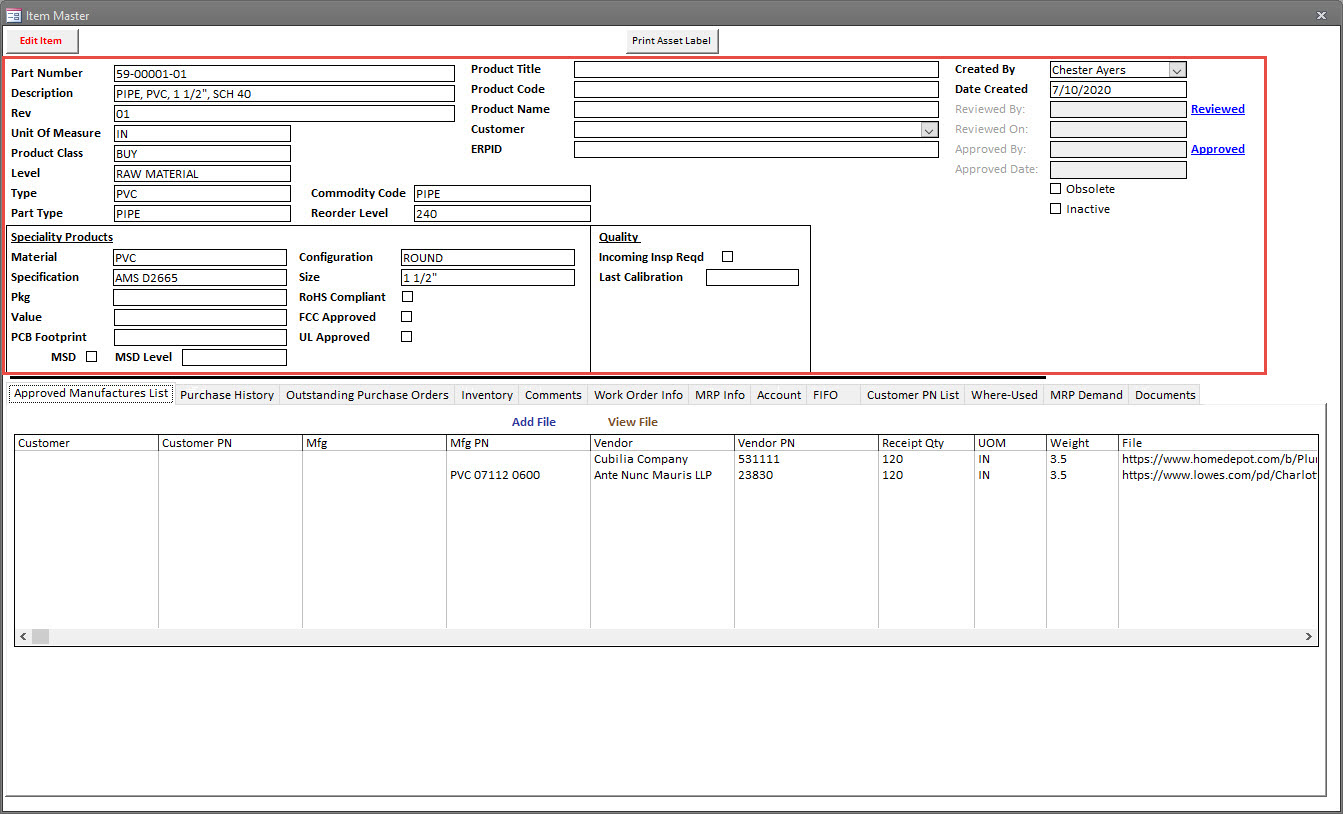
Call Now for a Free DEMO!
858-335-6421