Inventory Management
Managing Inventory drives the maximum amount of profit and customer satisfaction by using the least amount of investment in stock by sharing information within different parts of their business in real-time. Organizations use this data to make more informed ordering decisions and create more accurate forecasts to meet future demand without ending up with excess stock. Book A DemoEffective inventory management is essential for manufacturing companies for a multitude of reasons:
Cost Control:
By managing inventory effectively, businesses can significantly reduce holding costs associated with warehousing, insurance, and spoilage. Additionally, it minimizes the risks of overstocking or running out of stock, both of which can incur hefty expenses.
Efficiency in Production:
Having the appropriate materials in the right quantities at the right time is vital for seamless production operations. Inadequate inventory management can result in production delays or halts, jeopardizing deadlines and overall productivity.
Cash Flow Optimization:
Excessive purchasing of raw materials can tie up cash that could be better utilized elsewhere in the organization. Conversely, insufficient purchasing can lead to production delays, impacting sales. Striking the right balance in inventory ensures that cash flow remains healthy and not unnecessarily constrained by inventory.
Customer Satisfaction:
It is crucial to have finished goods readily available when customers need them to maintain high levels of customer satisfaction. Inventory-related delays can result in lost sales or customer dissatisfaction, which can negatively affect the company’s reputation.
Supply Chain Coordination:
Inventory is a key component of a broader supply chain. Effective inventory management guarantees that raw materials are accessible to suppliers, facilitating a steady flow of production materials and preventing bottlenecks or disruptions.
Demand Forecasting:
By scrutinizing inventory data, companies can enhance their ability to predict demand and adjust production schedules accordingly, leading to more precise ordering and reduced waste.
Lean Manufacturing Practices:
Strong inventory management aligns with lean principles by minimizing waste, such as surplus inventory or unnecessary material movement. This enables companies to boost efficiency and cut unnecessary costs.
Compliance and Traceability:
In certain industries, maintaining precise inventory records is vital for regulatory compliance. In instances of recalls or quality concerns, a well-organized inventory system can swiftly trace affected batches.
Overall, effective inventory management empowers manufacturers to operate more efficiently, reduce costs, enhance customer satisfaction, and remain competitive in a rapidly evolving market.
That is why Inventory Management Module is included in SimpleManufacturing™!
Our Inventory Management Features
Multiple Inventory Locations
Raw Material
Work-In-Process
Finished Goods
Scrap
Excess and Obsolete
First In, First Out (FIFO)
Ensure Inventory is Consumed using a first in, first out (FIFO) inventory management method
Actual Costing Method
FIFO Inventory Method identifies the Actual Cost of Each Item in Inventory. Standard, Last and Average Cost of Each Item is also Manage
Automated Material Transfers
Work Order Processing Transfers Inventory Automatically generating behind-the-scenes transaction records providing full accountability
Complete Transaction History
Behind-the-scenes processing records all inventory transactions from receipt to consumption
Manual Material Adjustments, Transfers
Manually adjust or transfer material generating behind-the-scenes transaction records providing full accountability
Unique Identification
Utilize Date Code, Lot Code, Expiration Date, Serial Number options to uniquely identify Inventory.
Cycle Counting
Utilize Proven Technics for Verification and Auditing of Inventory to Maintain Accuracy of Critical, High-Risk Items
Reports / Real-Time Data
Numerous reports and views showing Inventory of Interest
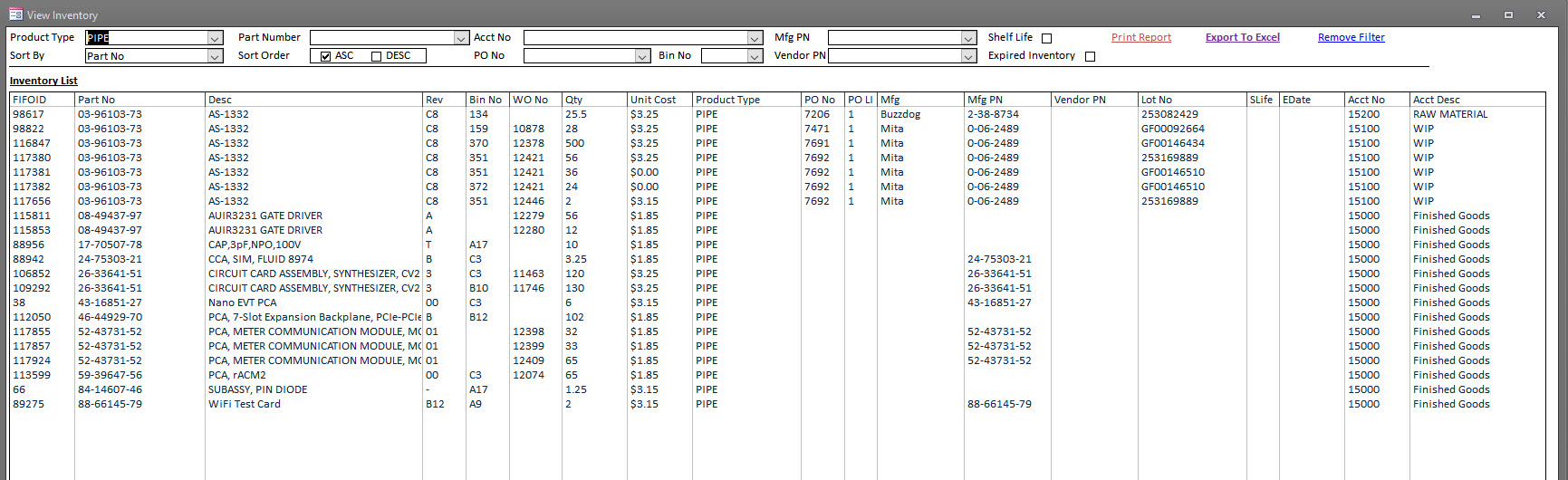
Call Now for a Free DEMO!
858-335-6421