Change Order Management
Streamline Your Success: Mastering Change Orders for Precision Manufacturing, using our Change Order Management module. Effective change order management ensures that changes are processed efficiently, accurately and thoroughly. Book A DemoChange Orders play a crucial role in the manufacturing process for several reasons:
Flexibility:
Manufacturing environments often need to adapt to changes in design, materials, or production methods. Change Orders provide a structured way to implement these adjustments without disrupting the overall workflow.
Quality Control:
By formally documenting changes, manufacturers can ensure that all modifications are reviewed, approved, and implemented correctly. This helps maintain product quality and consistency.
Cost Management:
Change Orders help track the financial impact of modifications. By evaluating the costs associated with changes, manufacturers can make informed decisions and avoid unnecessary expenses.
Communication:
Change Orders serve as a communication tool between different departments, such as engineering, production, and procurement. They ensure that everyone is aware of and agrees to the changes being made.
Compliance and Traceability:
Regulatory requirements and industry standards often mandate thorough documentation of changes. Change Orders provide a clear audit trail, ensuring compliance and making it easier to trace the history of modifications.
Risk Management:
By carefully evaluating and approving changes, manufacturers can identify potential risks and develop strategies to mitigate them. This helps avoid costly errors and production delays.
Continuous Improvement:
Change Orders facilitate a culture of continuous improvement by enabling manufacturers to refine processes, products, and systems based on feedback and new information.
In short, Change Orders are vital for maintaining efficiency, quality, and agility in the manufacturing process. They ensure that changes are managed systematically and communicated effectively, ultimately contributing to the overall success of the operation.
The Change Order Process in manufacturing is a structured approach to managing modifications to a product’s design or manufacturing procedure. Here’s a brief overview:
Identification of Change:
The process begins when an issue is identified on the manufacturing line, such as a defect or inefficiency, or for a product change introduced internally, Customers or Supplier or Vendor.
Change Order or Request:
A Change Order or Request (CO / CR) is submitted, detailing the proposed modifications.
Review and Approval:
The change order or request is reviewed by key stakeholders, including engineering and manufacturing teams. This step ensures that the proposed changes are feasible and beneficial.
Documentation:
Once approved, the change is documented, which includes details like affected components, revised drawings, and implementation instructions. This is where many manufacturing companies fail – It is important that all actions required of the change are clearly and accurately documented.
Implementation:
The changes are implemented. This is where many manufacturing companies fail – Not completing ALL Changes that were required. Either not all of the required changes are identified or the actions required are not fully executed or they are misunderstood or misinterpreted.
Verification:
After implementation, the changes are verified to ensure they resolve the identified issue without introducing new problems, and they have been completed fully and accurately.
Feedback Loop:
Information from the change process is fed back into the design process to inform future iterations and improvements.
Effective change order management ensures that changes are processed efficiently and that the final product meets all quality and performance requirements
The effectiveness and thoroughness of a closed loop Change Order process matters.
That is why it is included in SimpleManufacturing™!
Our Change Order Management Features
Bill of Material Changes
Clear, Concise and Easy process for Identifying New and Deleted Line Items and Line Item Changes
Router / Process Flow Changes
Clear, Concise and Easy process for Identifying New and Deleted Operational Steps and Operational Step Changes
Action List
Identify All Actions Required by the Change Order, Assign Action Owner and Action Due Date
Impact Of Changes
Automatic Identification of Sales Orders, Purchase Orders, Work Orders and Inventory Potentially Impacted By Change
Automatic Change Updating
Automatically update BOMs, Selected Sales Orders, Purchase Orders, Work Orders and Inventory with Change
Robust Reporting
Generate detailed reports of Change Orders, Actions and Change Details.
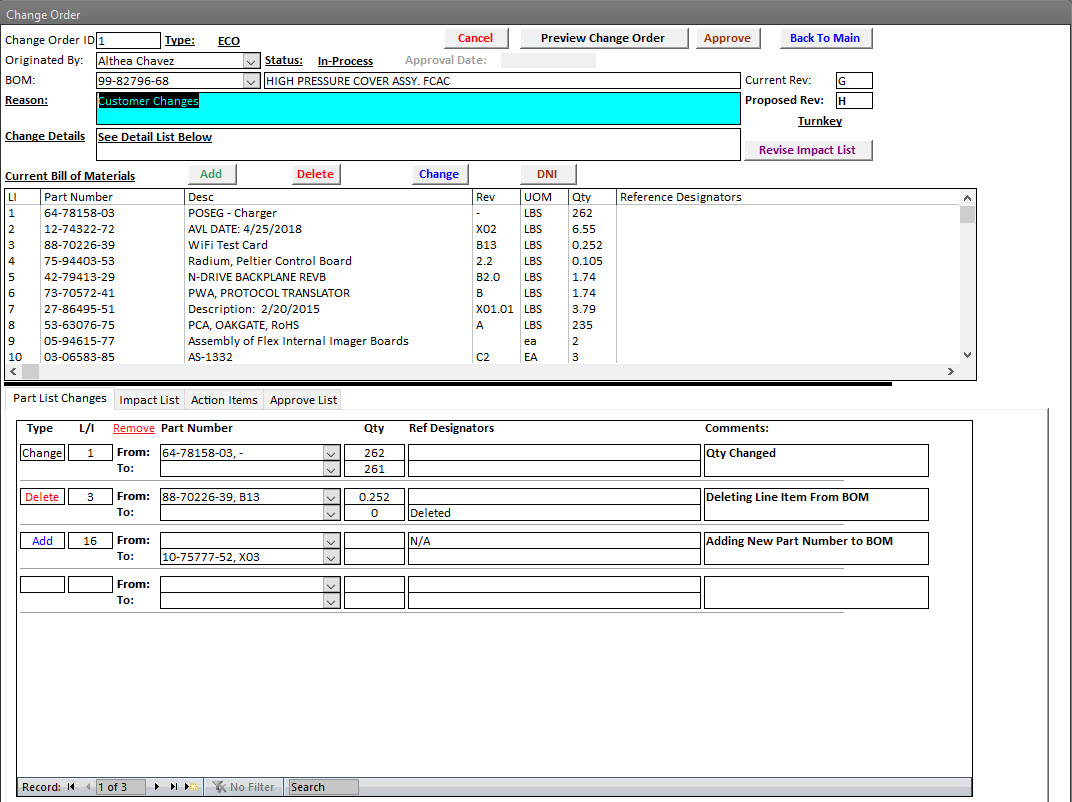
Call Now for a Free DEMO!
858-335-6421