Corrective Action Management
Recording and Managing Corrective Actions with EaseCentralized approach makes it easy to consistently create corrective actions, facilitate progress through the root cause analysis process, document the actions planned and taken to prevent recurrence, verify the implementation of those actions, and record the effectiveness of these actions to prevent recurrence
in our Corrective Action Management module.
Corrective actions in manufacturing refer to processes that companies put in place to identify, address, and eliminate issues that can cause product defects, operational inefficiencies, or safety hazards. Here’s a quick overview:
Types of Corrective Actions:
Root Cause Analysis (RCA):
This involves identifying the underlying causes of a problem to prevent recurrence. Common techniques include the “5 Whys” and Fishbone Diagrams.
Immediate Corrective Actions:
These are quick fixes applied to address immediate issues. They’re not always permanent solutions but are necessary to control the problem quickly.
Preventive Actions:
Preventive actions focus on identifying potential issues before they arise and implementing strategies to avoid them. This often involves reviewing and improving current processes.
Process Improvement:
Continuous improvement methods like Six Sigma and Lean Manufacturing can be used to optimize processes, reduce waste, and enhance product quality.
Employee Training:
Training employees on best practices, quality standards, and safety measures can prevent issues and improve overall efficiency.
Key Steps in Implementing Corrective Actions
Identify the Problem:
Utilize data from inspections, audits, and customer feedback.
Analyze the Root Cause:
Use RCA techniques to find the underlying cause of the issue.
Develop a Plan:
Create a detailed action plan with specific steps, responsibilities, and timelines.
Implement the Plan:
Execute the plan and monitor progress to ensure the actions are effective.
Review and Adjust:
Continuously review the actions taken and make adjustments as needed to prevent future issues.
Document and Communicate:
Document the entire process, including findings and actions taken, and communicate them to all relevant stakeholders.
By systematically applying corrective actions manufacturers can improve product quality enhance efficiency and ensure a safer working environment.
Since a Corrective Action Procedure is 1 of 5 required documented procedures of ISO900x and AS9100,
That is why it is included in SimpleManufacturing™!
Our Corrective Action Management Features
Common CA Information
Initiated By, Recipient, Owner, Problem / Issue Details, 8D Workflow Process Utilized
Root Cause Analysis
5 Whys Method Utilized, Identify Owner of RCA process with timeline
More Detailed CA Options
Part Number, Work Order, Customer, Supplier, Purchase Order Number, and Sales Order Number can be used when applicable
Assign and Manage Action Items
Assign Actions, Action Owner and Timeline during the Entire CA Process.
Link Files
Link Drawings, Specifications, NonConformances, Emails, etc. Add Evidence of Action Incorporated and Verification Actions Effective
SCAR Excel Template
Single-Click Feature to Populate Excel Template and Email to Suppliers to Identify Root Cause, Actions and Verification Outcomes
Import Supplier Response
Single-Click To Import Suppliers Root Cause, Actions and Verification Details into Corrective Action.
Containment Details
Ability to Identify Product, Areas with Known Issue and Actions Required
Single-Click Emails
Email Recipient, Owner, Initiator, Actions
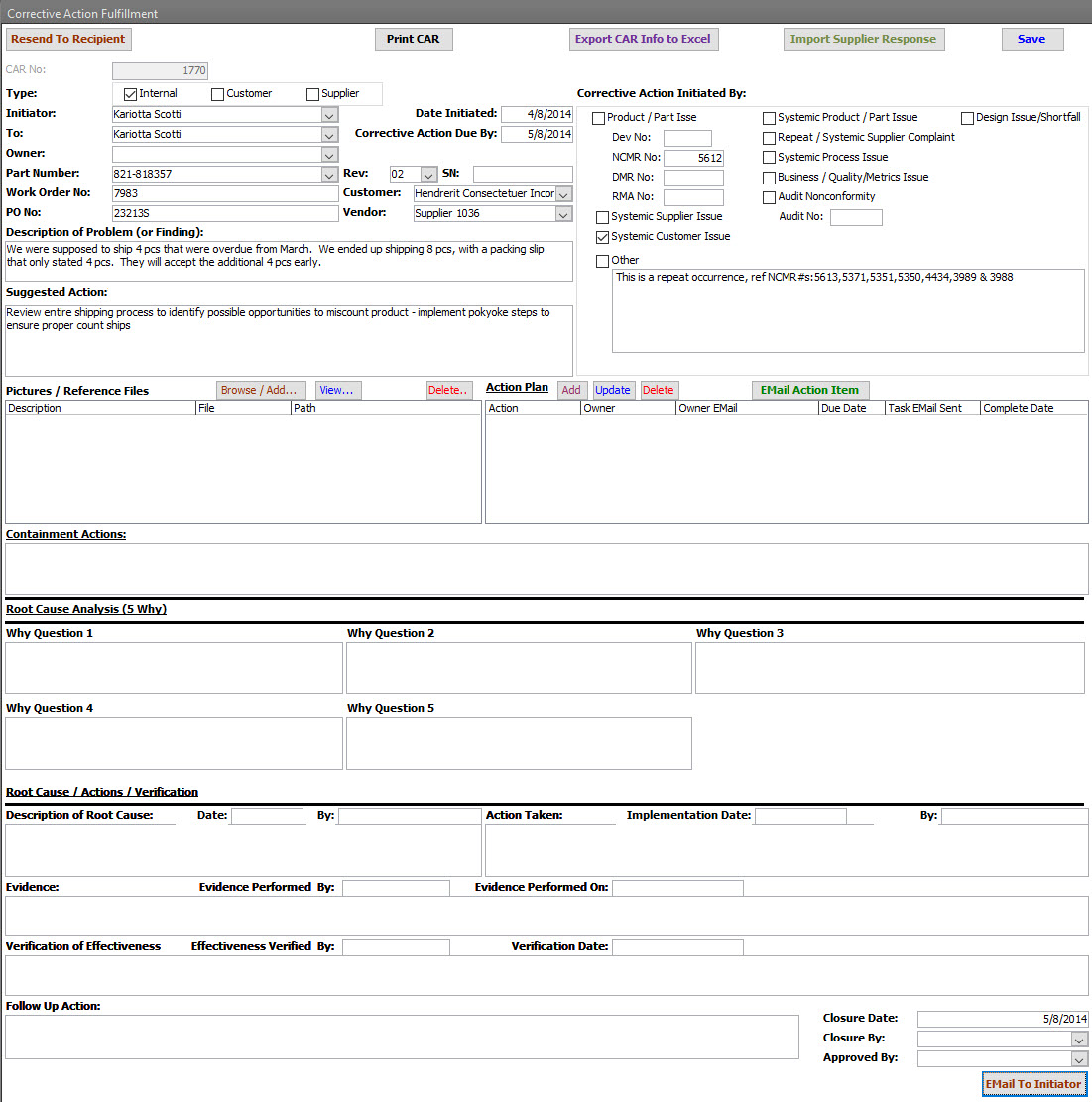
Call Now for a Free DEMO!
858-335-6421